There’s a synthetic rubber known for its resistance to oil, fuel, and chemicals – nitrile rubber, also called NBR. Derived from acrylonitrile and butadiene, this material has a wide range of uses in industries like automotive, aeronautical, medical, and nuclear. With properties like good resistance to oils and acids, superior strength, and stability in temperatures ranging from -40 to 108°C, nitrile rubber is a versatile material for various applications. From disposable gloves to automotive belts and seals, this article explores into the production, properties, and applications of nitrile rubber, shedding light on its importance in modern industries.
History
For over nine decades, nitrile rubber has been an crucial material in various industries, revolutionizing the creation of products that require resistance to chemicals and extreme temperatures.
Any discussion of nitrile rubber would be incomplete without exploring its meticulous production process. An intriguing blend of emulsifiers, activators, and catalysts is combined in polymerization vessels to create the versatile material.
History reveals that nitrile rubber production has evolved over the years. From the early days of commercial production in Germany in 1935 to the modern processes involving the addition of radical-generating activators and catalysts, the production of nitrile rubber has become more refined and efficient.
Production
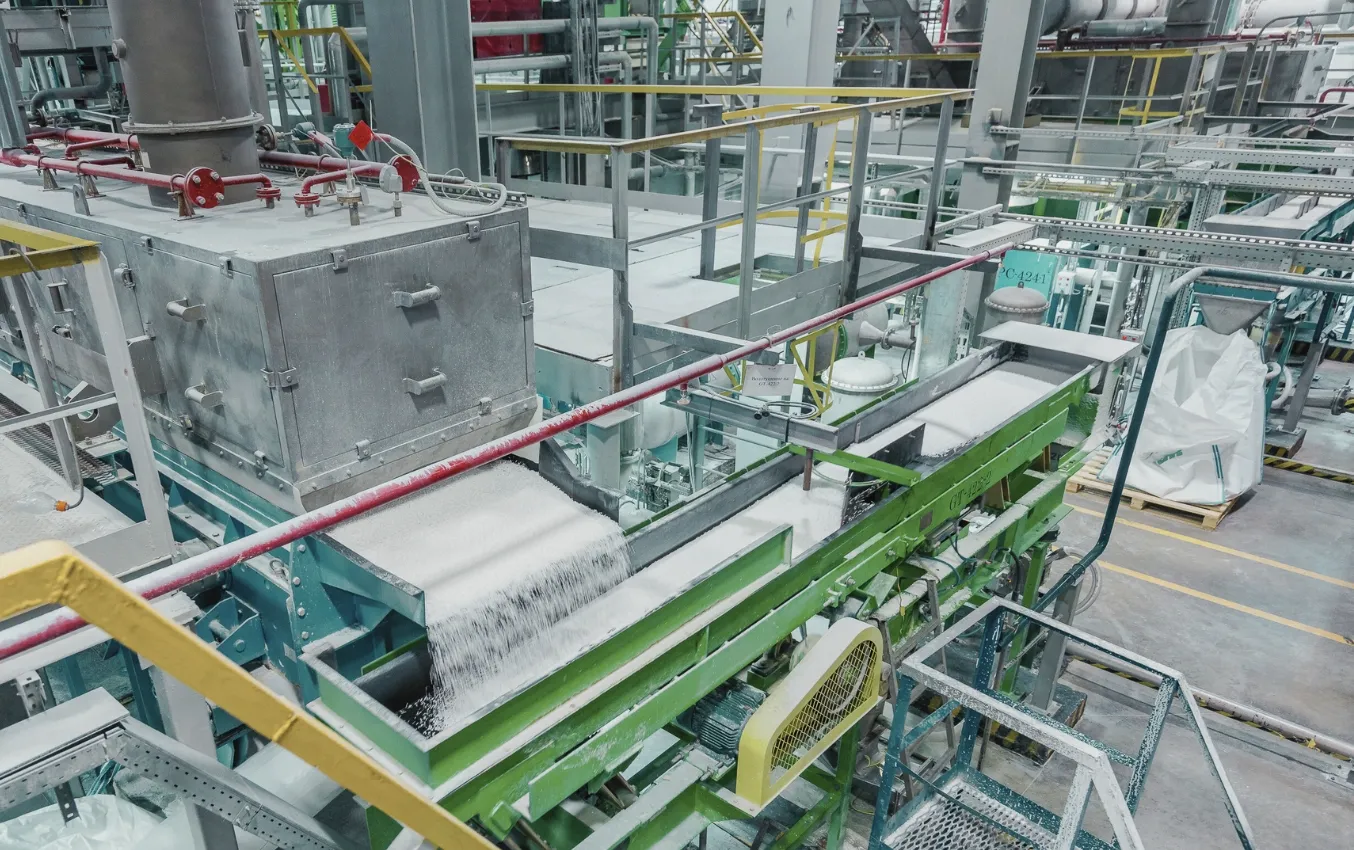
Hot NBR Production
To produce hot NBR, emulsifier, acrylonitrile, butadiene, radical generating activators, and a catalyst are added to polymerization vessels. The tanks are heated to 30–40 °C to facilitate the polymerization reaction. Once the latex is formed, it is stabilized with an antioxidant before coagulation.
Cold NBR Production
Any detailed information on the process for the production of cold NBR is scarce. However, the main difference from hot NBR production is that polymerization tanks are cooled to 5–15 °C instead of heated up to 30–40 °C.
Cold NBR production typically results in less branching on polymers compared to hot NBR. The amount of branching distinguishes the two types of NBR. Lower temperature conditions in cold NBR production may affect the overall properties and applications of the rubber compared to hot NBR.
Properties
Physical Properties
Properties of nitrile rubber include a tensile failure stress of 500-2500 PSI and elongation after fracture of 600% maximum. Its density can be compounded around 1.00 g/cm3, and its hardness, Shore A, ranges from 30-90.
Chemical Resistance
An important aspect of nitrile rubber is its resistance to mineral oils, benzene/petrol, ordinary diluted acids, and alkalines. It also has good resistance to vegetable oils. This property makes nitrile rubber an ideal material for applications where exposure to these substances is common.
ACN Content
Chemical composition plays a significant role in the properties of nitrile rubber. The ratio of acrylonitrile groups to butadiene groups, known as the ACN content, impacts the material’s resistance to nonpolar solvents. An ACN content of 33% is often used in applications requiring both solvent resistance and low-temperature flexibility.
Applications
Industrial Uses
The industrial uses of nitrile rubber are diverse, with applications ranging from automotive transmission belts to synthetic leather. The material’s resistance to oils and acids makes it ideal for use in industrial settings where durability and chemical resistance are crucial.
Automotive Industry
In the automotive industry, nitrile rubber is a popular choice for manufacturing O-rings, gaskets, oil seals, and V belts. Its high physical strength and resistance to heat, oil, and chemicals make it a valuable material for various automotive components, such as timing belts and dampers.
In the automotive industry, nitrile rubber is widely used for manufacturing O-rings for air-conditioning systems and other automotive components. Its excellent resistance to common automotive fluids and broad temperature range make it an ideal material for demanding automotive applications.
Medical and Food Service Industry
On the other hand, in the medical and food service industries, nitrile rubber is used to produce protective gloves due to its stability at temperatures ranging from −40 to 108 °C. The material’s resistance to oils, acids, and other chemicals provides protection for professionals in these industries.
Automotive air-conditioning systems rely on nitrile rubber O-rings for durability and longevity, highlighting the importance of this material in the automotive industry. Its resistance to heat, oil, and chemicals makes it a preferred choice for a wide range of automotive applications.
Hydrogenated Nitrile Butadiene Rubber (HNBR)
All hydrogenated nitrile butadiene rubber (HNBR) is produced through the hydrogenation of NBR. This process removes the vulnerable olefinic groups, leaving the nitrile groups unaffected. The degree of hydrogenation determines the type of vulcanization that can be applied to the polymer.
Properties
Nitrile rubber typically has tensile strengths of 20-31 MPa at 23°C. Compounded HNBR can be used over a broad temperature range, from -40°C to 165°C, with minimal degradation over time. Low ACN grades are used for low-temperature performance, while highly saturated HNBR grades with white fillers enhance high-temperature capabilities.
Applications
One of the main applications of hydrogenated nitrile butadiene rubber (HNBR) is in the automotive industry for dynamic and static seals, hoses, and belts. It is also widely used in industrial sealing applications for oil field exploration and processing, as well as in rolls for steel and paper mills.
Carboxylated Nitrile Butadiene Rubber (XNBR)
One alternative version of NBR is carboxylated nitrile butadiene rubber (XNBR), a terpolymer of butadiene, acrylonitrile, and acrylic acid. The presence of acrylic acid introduces carboxylic acid groups, allowing for crosslinking through the addition of zinc additives. The carboxyl groups are present at levels of 10% or less, along with traditional sulfur vulcanization.
Properties
On a volume basis, XNBR has tensile strength ranging from 20-31 MPa at 23 °C, offering excellent resistance to common automotive fluids like engine oil, coolant, and fuel. Compounding techniques allow for broad temperature range usage with minimal degradation over time.
Properties: Carboxylated nitrile butadiene rubber (XNBR) is known for its physical strength and retention of properties after long-term exposure to heat, oil, and chemicals. With tensile strength ranging from 20-31 MPa at 23 °C, XNBR has excellent resistance to automotive fluids and offers a broad temperature range for applications.
Applications
Any dynamic and static seals, hoses, and belts in the automotive and industrial sectors can benefit from the unique properties of XNBR. Its wide adoption in various applications, such as oil field exploration, processing, and industrial sealing, speaks to its effectiveness and versatility.
Butadiene: XNBR, also known as carboxylated nitrile butadiene rubber, is a versatile material used in dynamic and static seals, hoses, and belts in the automotive and industrial sectors. Its ability to withstand exposure to heat, oil, and chemicals make it valuable for applications in oil field exploration, processing, and industrial sealing.
Now that we have explored into the world of nitrile rubber, it is evident that this synthetic rubber is a versatile and resilient material widely used in various industries due to its resistance to chemicals, oils, and extreme temperatures. From automotive and aeronautical applications to medical and industrial uses, nitrile rubber’s properties make it a valuable component in many products. The development, production, and different types of nitrile rubber, such as HNBR and XNBR, showcase the ongoing advancements in rubber technology and innovation.